R. Sarjahani, M. Sheikhattar, S. Javadpour, B. Hashemi,
Volume 13, Issue 1 (3-2016)
Abstract
Surface smoothness of ceramic glazes is always an important characteristic of ceramic glazes as a point of surface engineering studies. Surface roughness affects chemical resistivity, glossiness and stainabiliy of glazes. In fact, less surface roughness improves cleanability of the surface by the least usage amount of detergents. In this investigation, surface topography of two common opaque glazes, zirconia and titania-based, has been investigated. Crystallinity of the surface has been studied from SEM images, and comparison of EDS elemental results with phase analysis results of XRD. Surface roughness profile measured by Marsurf M300, shows that titania-based glaze is almost 24% percentage more smooth than zirconia based glaze. Surface smoothness is in relation with crystallinity of glaze surface, crystal type and crystal distribution in amorphous matrix phase
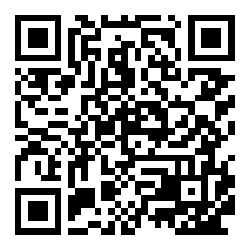
Amir Mostafapour, Milad Mohammadi, Ali Ebrahimpour,
Volume 18, Issue 2 (6-2021)
Abstract
A full factorial design of experiment was applied running 36 experiments to investigate the effects of milling parameters including cutting speed with three levels of 62.83, 94.24 and 125.66 m/min, feed rate with three levels of 0.1, 0.2 and 0.3 mm/tooth, cutting depth with two levels of 0.5 and 1 mm and machining media with two levels, on surface integration properties of magnesium AZ91C alloy such as grain size, secondary phase percent, surface microhardness and surface roughness. In all cases, a fine grained surface with higher secondary phase sediment and microhardness obtained comparing the raw material. According to analysis of variance results, the most effective parameter on grain size, secondary phase percent and microhardness was cutting depth and the most effective parameter on surface roughness was feed rate. although the grain size in all machined samples was smaller than that of the raw material but due to the dual effect of cryogenic conditions, which both cool and lubricate and reduce the temperature and strain rate at the same time, the direct effect of this parameter on grain size was not significant. Also, the all interaction effects of parameters on grain size and microhardness were significant.