Showing 27 results for Mg
Aneziris C.g., Borzov D., Schmidt G.,
Volume 2, Issue 1 (3-2005)
Abstract
Improved structures of MgO carbon bonded materials due to new binder systems and due to the application of electrical currents during operation have been achieved for advanced applications in the secondary metallurgy and during near net shape metal casting.
S. Ahmadi,, H. R. Shahverdi*, S. S. Saremi,
Volume 7, Issue 4 (10-2010)
Abstract
Abstract: In this research work, crystallization kinetics of Fe55Cr18Mo7B16C4 alloy was evaluated by X-ray diffraction, TEM observations and differential scanning calorimetric tests. In practice, crystallization and growth mechanisms were investigated using DSC tests in four different heating rates. Results showed that a two -step crystallization process occurred in the alloy in which - Fe phase was crystallized in the first step after annealing treatments. Activation energy for the first step of crystallization i.e. - Fe was measured to be 276 (kj/mol) according to Kissinger model. Further, avrami exponent calculated from DSC curves was 2 and a three -dimensional diffusion controlled mechanism with decreasing nucleation rate was observed in the alloy. It is also known from the TEM observations that crystalline á – Fe phase nucleated in the structure of the alloy in an average size of 10 nm and completely mottled morphology.
H. Momeni, H. Razavi, S. G. Shabestari,
Volume 8, Issue 2 (6-2011)
Abstract
Abstract: The supersolidus liquid phase sintering characteristics of commercial 2024 pre-alloyed powder was studied at different sintering conditions. Pre-alloyed 2024 aluminum alloy powder was produced via air atomizing process with particle size of less than 100 µm. The solidus and liquidus temperatures of the produced alloy were determined using differential thermal analysis (DTA). The sintering process was performed at various temperatures ranging from the solidus to liquidus temperatures in dry N2 gas atmosphere for 30 min in a tube furnace. The maximum density of the 2024 aluminum alloy was obtained at 610ºC which yields parts with a relative density of 98.8% of the theoretical density. The density of the sintered samples increased to the maximum 99.3% of the theoretical density with the addition of 0.1 wt. %Sn powder to the 2024 pre-alloyed powder. The maximum density was obtained at 15% liquid volume fraction for both powder mixtures.
B. Mehrabi, M. Abdellatif, F. Masoudi,
Volume 8, Issue 2 (6-2011)
Abstract
Abstract: Ore mineral characterization and various experimental testwork were carried out on Asian Abe-Garm dolomite, Qazvin province, Iran. The testwork consisted of calcining, chemical characterization, LOI determination, and reduction tests on the calcined dolomite (doloma), using Semnan ferrosilicon. Calcining of dolomite sample was carried out at about 1400 ºC in order to remove the contained CO2, moisture, and other easily volatilised impurities. The doloma was milled, thoroughly mixed with 21% Semnan ferrosilicon and briquetted in hand press applying 30 MPa pressure. The briquettes were heated at 1125-1150 ºC and 500Pa in a Pidgeon-type tube reactor for 10-12 hours to extract the magnesium. Ferrosilicon addition, relative to doloma, was determined based on the chemical analyses of the two reactants using Mintek’s Pyrosim software package. Magnesium extraction calculated as 77.97% and Mg purity of 96.35%. The level of major impurities in the produced magnesium crown is similar to those in the crude metal production.
M. S. Kaiser, A. S. W. Kurny,
Volume 8, Issue 4 (12-2011)
Abstract
Microstructure and properties of the Al-6Si-0.3Mg alloys containing scandium (0.2 to 0.6wt %) were investigated. The microstructure was observed by optical microscopy, the hardness was determined by Vickers tester and phase transformation was investigated by differential scanning calorimetry (DSC) technique. The results showed that scandium can refine dendrites, enhance hardness in the aged alloys and suppress softening effect during prolonged ageing treatment.
Sh. Shahriari, M. Ehteshamzadeh,
Volume 10, Issue 1 (3-2013)
Abstract
Abstract: Plasma electrolytic oxidation (PEO) technique was used to prepare ceramic coatings on the casted aluminum alloys containing ~5 and ~9.5 wt.% Mg. The applied voltage was controlled at 450V and 550V for evaluating the effect of this main parameter, as well as, magnesium content of the substrate on the microstructure and electrochemical corrosion behavior after PEO treating. The results of X-ray diffraction confirmed formation of galumina and MgSiO3. It was found that higher applied voltage caused fewer and minor discharge channels which led to higher corrosion resistance. Also, increasing of magnesium content of the substrate caused decreasing of polarization resistance, which could be associated to the formation of MgSiO3.
S. Ahmadi, H. R. Shahverdi,
Volume 10, Issue 4 (12-2013)
Abstract
Crystallization kinetics of Fe52Cr18Mo7B16C4Nb3 alloy was evaluated using X-ray diffraction, differential scanning calorimetric (DSC) tests and TEM observations in this research work. In effect, crystallization and growth mechanisms were investigated using DSC tests in four different heating rates (10, 20, 30, 40 K/min) and kinetic models (i.e. Kissinger- Starink, Ozawa, and Matusita methods). Results showed that a two -step crystallization process occurred in the alloy in which α - Fe and Fe3B phases were crystallized respectively in the structure after heat treatment. Activation energy for the first step of crystallization i.e., α - Fe was measured to be 421 (kj/mol) and 442 (kj/mol) according to both Kissinger- Starink and Ozawa models respectively. Further, Avrami exponent calculated from DSC curves was 1.6 and a two -dimensional diffusion controlled mechanism with decreasing nucleation rate was observed in the alloy. TEM observations reveal that crystalline α – Fe phase nucleated in the structure of the alloy in an average size of 10 nm and completely mottled morphology
M. S. Kaiser,
Volume 11, Issue 4 (12-2014)
Abstract
The evaluation of texture as a function of recrystallization has been characterized for directly cold rolled Al-6Mg, Al-6Mg-0.4Sc and Al-6Mg-0.4Sc-0.2Zr alloys. Samples were annealed isothermally at 400 °C for 1 to 240 minutes to allow recrystallization. Recrystallization kinetics of the alloys is analyzed from the micro-hardness variation. Isothermally annealed samples of aluminum alloys were also studied using JMAK type analysis to see if there exists any correlation between the methods. Recrystallization fraction behavior between two methods the scandium added alloys show the higher variation due to precipitation hardening and higher recrystallization behavior. The scandium and zirconium as a combined shows the more variation due to formation of Al3(Sc, Zr) precipitate. From the microstructure it is also observed that the base Al-Mg alloy attained almost fully re-crystallized state after annealing at 400 °C for 60 minutes
S. Ahmadi, H. R. Shahverdi,
Volume 12, Issue 2 (6-2015)
Abstract
Crystallization of α – Fe phase during annealing process of Fe55Cr18Mo7B16C4 bulk amorphous alloy has
been evaluated by X- ray diffraction, differential scanning calorimetric tests and TEM observations in this research.
In effect, crystallization mechanism and activation energy of crystallization were evaluated using DSC tests in four
different heating rates (10, 20, 30, 40 K/min). A two -step crystallization process was observed in the alloy in which
α–Fe phases was crystallized in the first step after annealing process. Activation energy for the first step of
crystallization process (i.e. α – Fe phase) was measured to be 276 (Kj/mole) according to Kissinger kinetic model.
Furthermore, Avrami exponent calculated from DSC curves was two and a three -dimensional diffusion controlled
mechanism with decreasing nucleation rate was observed in the alloy. It is also known from the TEM observations that
crystalline α – Fe phase nucleated in the structure of the alloy in an average size of 10 nm and completely mottled
morphology
E. Khoshomid Aghdam, R. Naghizadeh, H. R. Rezaie,
Volume 12, Issue 3 (9-2015)
Abstract
MgAl2O4/Ti(C,N) composites were synthesized through aluminothermic reaction between Al,TiO
2,MgO
powders and phenolic resin in coke bed condition. Effect of addition of carbon black and sugar into the mixture at
different temperatures were investigated. The phases and microstructures of samples were investigated by X-ray
diffraction (XRD) and scanning electron microscopy (SEM). MgAl
2O4
/Ti(C,N) composites without additive were
obtained after heat treatment at 1600˚C. With addition of carbon black TiC, TiN and Ti(C,N) were appeared after firing
at 1400˚C and formation of spinel/Ti(C,N) composites were completed at 1600˚C. In sample containing sugar,
MgAl2O4
-Ti(C,N) composite were completely synthesized at 1400˚C. In this sample crystallite size of Ti(C,N) were 32
nm and carbon content of titanium carbonitride (Ti(C,N)) reached to 0.442 value.
M. Ershadi Khameneh, H. Shahverdi, M. M. Hadavi,
Volume 12, Issue 4 (12-2015)
Abstract
Creep age forming (CAF) is one of the novel methods in aerospace industry that has been used to manufacture components of panels with improved mechanical properties and reduced fabrication cost. CAF is a combined age-hardening and stress-relaxation that are responsible for strengthening and forming, respectively. This paper deals with the experimental investigations of mechanical and springback properties of Al-Zn-Mg Al alloy in creep forming process. Creep forming experiments have been performed at temperatures of 120◦C and 180◦C for 6–72 h. Results indicated that yield stress and hardness of creep age formed specimens increased with increasing forming time and temperature, simultaneously induced deflection by stress-relaxation increased. Incorporating spring back and mechanical properties, it can be found that the appropriate forming cycle was 180 ◦C/24 h among all forming conditions. CAF Time increase to a certain extent increased mechanical properties. This can be attributed to presence of stress in CAF that causes the precipitates be finer because of creation more nucleation sites. Therefor the growth of precipitates, takes place at long time and postpones the decreasing of the yield stress
M. Khosravi Saghezchi, R. Ajami, M. Biazar Markie, H. Sarpoolaky,
Volume 12, Issue 4 (12-2015)
Abstract
A comparing study on formation and microstructure features of aluminum titanate is investigated through both solid-state and sol-gel processes. Aluminum titanate formed by firing at 1350ºC and 1450ºC for 4h in solid-state process. In the sol-gel process formation of submicron sized particles is followed by addition of sucrose into the transparent sol. XRD analysis was confirmed the formation of aluminum titanate at 1400ºC in lower duration of calcination (3h) without any additives in the sol-gel process. In this work 2wt% MgO is added to the samples as the additive for forming acceleration of aluminum titanate. The influence of MgO addition and heat treatment are studied on phase formation and microstructure development of aluminum titanate in both procedures. Additive optimizes aluminum titanate formation at lower temperatures (1300-1350ºC). Phase and microstructure studies of Mg containing samples optimally show significance in aluminum titanate formation.
M.h. Avazkonandeh-Gharavo, M. . Haddad-Sabzevar, H. Fredriksson,
Volume 13, Issue 2 (6-2016)
Abstract
Because the partition coefficient is one of the most important parameters affecting microsegregation, the aim of this research is to experimentally analyse the partition coefficient in Al-Mg alloys. In order to experimentally measure the partition coefficient, a series of quenching experiments during solidification were carried out. For this purpose binary Al-Mg alloys containing 6.7 and 10.2 wt-% Mg were melted and solidified in a DTA furnace capable of quenching samples during solidification. Cooling rates of 0.5 and 5 K/min were used and samples were quenched from predetermined temperatures during solidification. The fractions and compositions of the phases were measured by quantitative metallography and SEM/EDX analyses, respectively. These results were used to measure the experimental partition coefficients. The resultant partition coefficients were used to model the concentration profile in the primary phase and the results were compared with equilibrium calculations and experimental profiles. The results of calculations based on the experimental partition coefficients show better consistency with experimental concentration profiles than the equilibrium calculations.
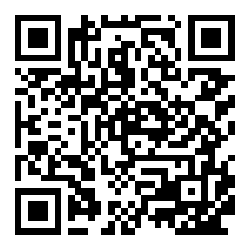
Z. Sadeghian, R. Dezfulizadeh,
Volume 13, Issue 2 (6-2016)
Abstract
In situ Al2024- Mg2Si composite was fabricated by spark plasma sintering (SPS) of reactive powder. Reactive powder was obtained from mechanical alloying (MA) of elemental powders. Clad layers of in situ composite were fabricated on Al substrates by spark plasma sintering (SPS). Structural evolution during MA process and after SPS was investigated by X-ray diffractometery (XRD). Scanning electron microscopy (SEM) was utilized to study the microstructure of sintered samples. Hardness and tensile behavior of sintered samples were investigated. The results showed that SPS of mechanically alloyed unreacted powder can result in the in situ formation of Mg2Si and Mg2Al3 within the Al matrix. SPSed clad layer showed a sound and clear interface to the Al substrate with a hardness of about 140 HV. Sintered in situ composite exhibited a tensile strength of 288 MPa.
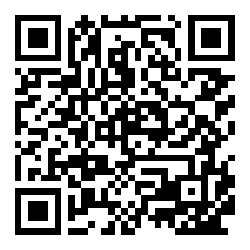
N. Aboudzadeh, Ch. Dehghanian, M.a. Shokrgozar,
Volume 14, Issue 4 (12-2017)
Abstract
Recently, magnesium and its alloys have attracted great attention for use as biomaterial due to their good mechanical properties and biodegradability in the bio environment. In the present work, nanocomposites of Mg - 5Zn - 0.3Ca/ nHA were prepared using a powder metallurgy method. The powder of Mg, Zn and Ca were firstly blended, then four different mixtures of powders were prepared by adding nHA in different percentages of 0, 1, 2.5 and 5 %wt. Each mixture of powder separately was fast milled, pressed, and sintered. Then, the microstructure and mechanical properties of the fabricated nanocomposites were investigated. The XRD profile for nanocomposites showed that the intermetallic phases of MgZn2, MgZn5.31 and Mg2Ca were created after sintering and the SEM micrographs showed that the grain size of nanocomposite reduced by adding the nHA. The nano composite with 1wt. % nHA increased the density of Mg alloy from 1.73 g/cm3 to 1. 75 g/cm3 by filling the pores at the grain boundaries. The compressive strength of Mg alloy increased from 295MPa to 322, 329 and 318MPa by addition of 1, 2.5 and 5wt. % nHA, respectively.
A. Eivani, S.h. Seyedein, M. Aboutalebi,
Volume 15, Issue 1 (3-2018)
Abstract
In this research, samples of AlMg0.7Si aluminum alloy are deformed up to three passes using equal channel angular pressing (ECAP). Formation of a sub-micron structure after three passes of ECAP is demonstrated. Microstructural stability of the samples is investigated at temperatures of 300-500 °C. At 300 °C, fine recrystallized structure forms after 10 min which remains stable when the annealing proceeds up to 18 hrs. However, at 350 °C and higher, the microstructure is quite unstable. Even by 10 sec annealing, the samples exhibit recrystallized structure which turned to abnormal grain growth when temperature enhances to 500 °C and time up to 300 sec.
M. H. Zamani, M. Divandari, M. Tamizifar,
Volume 15, Issue 1 (3-2018)
Abstract
Lap joints of commercially pure magnesium plates to aluminium plates (Magnesium plate on the top, and Aluminium plate, grade 1100, on the bottom side) were conducted by friction stir welding using various traveling and rotation speeds of the tool to investigate the effects of the welding parameters on the joint characteristics and strength. Defect-free lap joints were obtained in the welding traveling speed range of 40-80 mm/min, and rotational speed range of 1200-1600 rpm. The shear tensile strength of Mg/Al joints increased as a result of decreasing the welding speed from 120 to 40 mm/min at constant rotation speed of 1600 rpm. Defects such as surface grooves, excessive flash, tunnels, and voids were observed if the joints prepared out of the mentioned range. The effects of the welding parameters are discussed metallographically based on observations with optical and scanning electron microscopes.
A. Beigei Kheradmand, S. Mirdamadi, S. Nategh,
Volume 17, Issue 3 (9-2020)
Abstract
In the present study, the effect of adding minor amounts of scandium and zirconium elements to the 7075 alloyon the re-crystallization behaviour of one aluminium alloy (7000 series) was investigated. For this purpose, two kinds of Al-Zn-Mg-Cu-Sc-Zr alloys with the same amount of Zr and different amount of Sc were prepared. Homogenization durations and temperatures of alloys after alloying were obtained by DSC analysis and optical microstructure observations. The results showed that the optimum homogenization temperatures for Al-Zn-Mg-Cu-0.05Sc-0.1Zr and Al-Zn-Mg-Cu-0.1Sc-0.1Zr alloys were 500
0C and 490
0C respectively, and the optimum duration for both alloys was 12hours. After homogenization of alloys, the re-crystallization behaviour of the alloys was investigated by Brinell hardness test. Obtained results showed that although the starting re-crystallization temperature for both alloys was similar in 2 hours, but it was 130°C for alloys with 30% forming, and 120°C for alloys with 50%forming and recrystallization temperature for Al-Zn-Mg-Cu-0.1Sc-0.1Zr alloy was 350

in 2 hours. Despite what was expected, the hardness of Al-Zn-Mg-Cu-0.05Sc-0.1
R. Niazi, E. Tohidlou, H. Khosravi,
Volume 17, Issue 3 (9-2020)
Abstract
The effects of erbium (Er) addition at various weight percentages (0-0.6 wt.% at an interval of 0.2) on the microstructural characteristics, tensile response and
wear properties of as-cast Al-7.5Si-0.5Mg alloy were evaluated. The microstructure of samples was examined by X-ray diffraction, optical microscopy and scanning electron microscopy. The obtained results demonstrated that the incorporation of erbium obviously decreased the α-Al grain size and eutectic Si, and altered the Si morphology from plate to semi-globular. Further addition of erbium (> 0.2 wt.%) did not alter the eutectic morphology and size. Moreover, the Al
3Er phase was also observed in the eutectic region after modification. Out of the erbium contents used, 0.2 wt.% erbium showed the best influence on the tensile and wear properties. Compared with those of unmodified specimen, the values of ultimate tensile strength and elongation were enhanced by 31% and 39%, respectively with the introduction of 0.2 wt.% erbium. Additionally, a remarkable enhancement in the wear properties was observed with the addition of 0.2 wt.% erbium.
M. Hamdi, H. Saghafian Larijani, S. G. Shabestari, N. Rahbari,
Volume 17, Issue 3 (9-2020)
Abstract
Aluminum matrix composites are candidate materials for aerospace and automotive industries owing to their specific properties such as high elastic modulus (E), improved strength and low wear rate. The effect of thixoforming process on the wear behavior of an Al-Mg2Si composite was studied in this paper. During applying thixoforming process, casting defects such as macrosegration, shrinkage and porosity are being effectively reduced. These advantages are sufficient to attract more exploration works of thixoforming operation. Thermal analysis of the composite, as-cast microstructure, wear surface and subsurface area of the thixoformed alloy were investigated. Wear behavior of the specimens were examined using a pin-on-disk machine based on ASTM-G99, at the applied loads of 25, 50 and 75 N and the constant sliding velocity of 0.25m/s. The worn surfaces and subsurfaces were examined by scanning electron microscopy (SEM). The experimental results indicated that the thixoformed specimens exhibited superior wear resistance than the as-cast alloy. Moreover, the dominant wear mechanism is an adhesive wear followed by the formation of a mechanical mixed layer (MML). However, a severer wear regime occurs in the as cast specimens compared with the thixoformed ones